Foam Cutting Machine
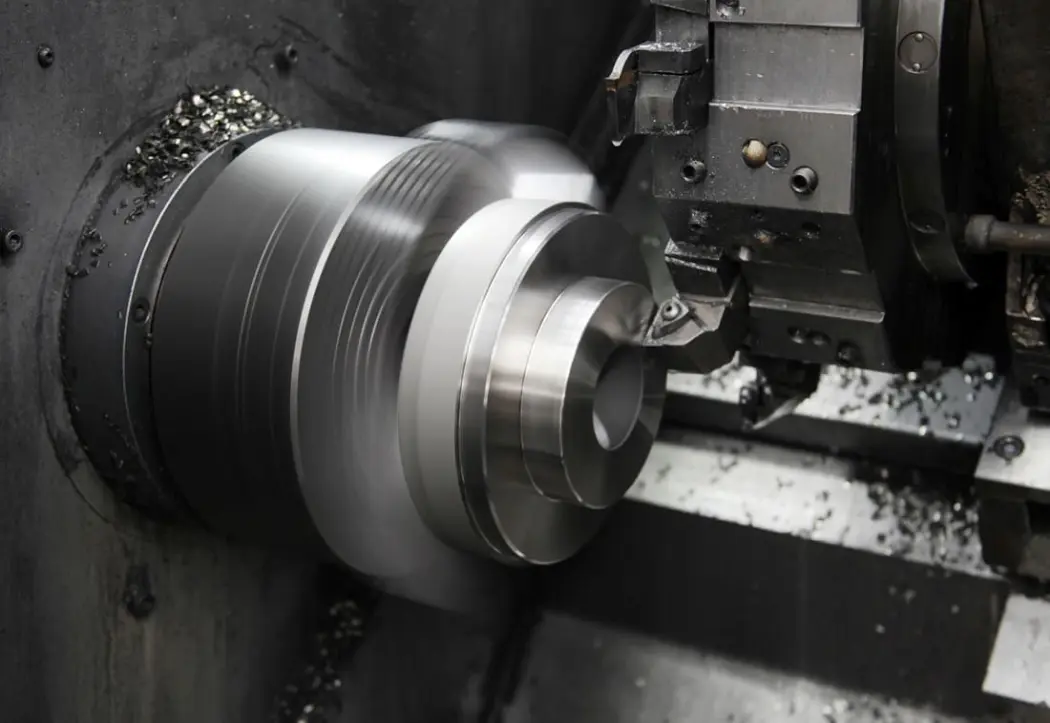
As we delve into the world of manufacturing and production, it becomes evident that foam cutting machines play a pivotal role in various industries. These machines are essential tools used to cut and shape foam materials into desired forms for different applications. From packaging to furniture manufacturing, automotive industry to construction, these machines have proven their worth by providing precise cuts, reducing waste, and increasing efficiency.
Understanding the Importance of Foam Cutting Machines in Various Industries
The importance of CNC foam cutting machine extends beyond just precision and efficiency. They also contribute significantly to cost savings. Traditional methods of cutting foam often result in material wastage due to inaccurate cuts or human error. However, with the advent of advanced foam cutting machines, industries can now achieve accurate cuts with minimal waste, leading to substantial cost savings in the long run. Moreover, these machines require less manual labor compared to traditional methods, further reducing operational costs.
Furthermore, the versatility of foam cutting machines is another factor that underscores their importance across various sectors. Whether it’s creating intricate designs for upholstery in the furniture industry or producing insulation materials for construction purposes, these machines can handle a wide range of tasks with ease. Their ability to work with different types of foams - such as polyurethane foam or polystyrene - adds another layer of flexibility that makes them indispensable in today’s fast-paced industrial landscape.
Types of Foam Cutting Machines and Their Key Features
There are several types of foam cutting machines available in the market, each designed to meet specific needs and applications. The most common ones include hot wire foam cutters, oscillating blade foam cutters, and laser foam cutters. Hot wire foam cutters use a heated wire to melt through the foam, creating smooth cuts with minimal dust. They are ideal for intricate designs and models but may not be suitable for thicker foams. Oscillating blade foam cutters, on the other hand, use a rapidly moving blade to slice through the material. These machines can handle thicker foams and offer more versatility in terms of shapes and sizes.
Laser foam cutters represent the pinnacle of precision and efficiency in this field. They utilize high-powered lasers to make precise cuts without physical contact with the material, reducing wear and tear on the machine while ensuring consistent results. However, they tend to be more expensive than other types of foam cutting machines due to their advanced technology. Each type of machine has its own set of key features that make it suitable for certain tasks. For instance, hot wire cutters often feature adjustable temperature controls for different types of foam materials while oscillating blade machines may come with interchangeable blades for various cutting requirements.
When considering these different types of foam cutting machines, it’s important to understand your specific needs and requirements. Factors such as the type of foam you’ll be working with, the complexity of your designs, your budget constraints, and your production volume should all play a role in determining which machine is right for you. By understanding these key features and how they align with your needs, you can make an informed decision that will enhance productivity while ensuring high-quality results.
Factors to Consider When Choosing the Right Foam Cutting Machine
When it comes to selecting the right foam cutting machine for your needs, there are several key factors that you should take into consideration. First and foremost, you need to consider the type of foam material you will be working with. Different types of foams require different cutting methods, so it’s crucial to choose a machine that is compatible with your specific materials. Additionally, the size and thickness of the foam pieces you plan on cutting also play a significant role in determining which machine is best suited for your operations.
Another important factor to consider is the volume of work that your business handles. If you’re running a large-scale operation that requires continuous foam cutting, then investing in a high-capacity, automated machine would be beneficial. On the other hand, if your production volume is relatively low or sporadic, a manual or semi-automatic foam cutter might suffice. Furthermore, keep in mind that higher-end machines often come with advanced features such as programmable controls and precision cutting capabilities which can significantly enhance productivity and efficiency.
Last but not least, don’t overlook the importance of ease-of-use and maintenance when choosing a foam cutting machine. A user-friendly interface can reduce training time and minimize errors during operation. Similarly, machines that are easy to maintain will have longer lifespans and lower repair costs over time. In conclusion, by carefully considering these factors - material compatibility, production volume, advanced features, ease-of-use and maintenance - you’ll be well-equipped to make an informed decision when purchasing your next foam cutting machine.
Step-by-Step Guide to Operating a Foam Cutting Machine for Optimal Results
Operating a foam cutting machine efficiently requires a clear understanding of the process and careful adherence to safety measures. The first step involves setting up the machine correctly. This includes ensuring that the machine is clean, free from any previous foam residues, and properly lubricated if necessary. It’s also crucial to check that all parts are in good working condition and securely fastened. Once this is done, you can then load your foam material onto the machine, making sure it’s well-aligned with the cutting blade.
The next step involves setting the correct parameters on your foam cutting machine. These parameters include the speed of the cut, depth of cut, and type of cut (straight or curved). It’s important to note that these settings will vary depending on the type of foam being used and the desired end product. Therefore, it’s advisable to refer to your machine’s manual or consult with an expert for precise settings. After setting up everything correctly, you can now start your machine and carefully monitor its operation.
Lastly, after completing your cuts, it’s essential to turn off your foam cutting machine properly and conduct post-operation maintenance. This includes cleaning up any leftover materials from the machine and inspecting it for any potential damage or wear that may have occurred during operation. Regular maintenance not only prolongs the lifespan of your equipment but also ensures consistent high-quality output in future operations. Remember that operating a foam cutting machine requires patience and practice; therefore don’t be discouraged if you don’t achieve optimal results immediately.
Common Challenges Faced and Solutions for Efficient Foam Cutting
Despite the numerous advantages of foam cutting machines, operators often encounter a few common challenges that can hinder efficient production. One such issue is the wear and tear of blades due to continuous use. Over time, this can lead to uneven cuts and reduced precision. To combat this, it’s crucial to regularly maintain and replace blades as needed. Additionally, using high-quality blades made from durable materials can significantly extend their lifespan and ensure consistent, precise cuts.
Another challenge faced in foam cutting is managing the heat produced during the process. Excessive heat can cause the foam to melt or deform, compromising the quality of the final product. This issue can be mitigated by using machines with advanced cooling systems or by operating at lower speeds to reduce heat generation. Furthermore, selecting appropriate foam types that are resistant to high temperatures can also help in maintaining product integrity.
The third common challenge is dealing with dust and debris generated during foam cutting. Not only does this create a messy work environment, but it can also pose health risks for machine operators if not properly managed. Implementing effective dust extraction systems is an essential solution for this problem. Regular cleaning schedules should also be maintained to keep the workspace clean and safe. By addressing these challenges head-on, businesses can ensure efficient operation of their foam cutting machines while producing high-quality products.
Future Trends and Innovations in Foam Cutting Machines for Enhanced Productivity
As we look towards the future, it’s clear that foam cutting machines will continue to evolve and improve. One of the most exciting trends is the integration of advanced technology such as artificial intelligence (AI) and machine learning. These technologies can help optimize the foam cutting process by predicting and adjusting for variables that could affect the quality of the cut. For instance, AI could analyze data from previous cuts to determine optimal speed and pressure settings, reducing waste and improving efficiency.
Another promising innovation in foam cutting machines is the use of robotics. Robotic arms can be programmed to perform precise cuts with a level of accuracy that surpasses human capabilities. This not only enhances productivity but also reduces the risk of errors, leading to higher quality products. Furthermore, robotic foam cutting machines can operate continuously without fatigue, significantly increasing output for businesses.
Lastly, sustainability is becoming an increasingly important factor in all industries, including foam cutting. Manufacturers are developing more energy-efficient machines and exploring ways to recycle or repurpose waste foam from the cutting process. Some companies are even researching biodegradable foams that could reduce environmental impact further. As these trends continue to develop, they promise a future where foam cutting machines are smarter, more efficient, and more sustainable than ever before.
Autor: Materiał partnera